TM 5-3805-260-24
AIR SYSTEM AND BRAKES
WARNING
Sudden movement of the machine or release
of air under pressure can cause injury to
persons on or near the machine. To prevent
possible injury, do the procedure that follows
before testing and adjusting the air system and
brakes:
1.
Move the machine to a smooth horizontal location.
Move away from working machines and personnel.
Stop the engine.
2. Permit only one operator on the machine. Keep all
other personnel either away from the machine or in
view of the operator.
3. Activate the parking and emergency brakes. Lower
the bowl to the ground. Put blocks in front of and
4.
Push on the brake pedal many times until there is no
more brake air pressure.
5. Make sure all air pressure is released before any
fitting, hose or component is loosened, tightened,
removed or adjusted.
NOTE: Before any operation checks are made, open the
drain valves to release any water in the air reservoirs.
Water lowers the capacity in the reservoirs and can
cause the air compressor to run constantly. Close the
drain valve. Start the engine and operate the machine
until it is at the normal temperature for operation.
VISUAL CHECKS
Before any operation checks are made to the air
system and brakes, visually inspect the complete system
as follows:
1. Check for cracks or wear in hoses and lines.
2. Check for restriction to flow; like sharp bends, clamps
that are not installed correctly, and damage to hoses
and lines.
3. Check for loose connections.
4. Check for damage to components.
OPERATION CHECKS
WARNING
Make reference to WARNING at the beginning
of AIR SYSTEM AND BRAKES TESTING AND
ADJUSTING section.
Operation checks of the air system and brakes can
be used to find the source of leakage in the system or to
make a diagnosis of bad performance.
Leakage Checks
Tools Needed:
8M2885 Pressure Gauge, 0 to 200 psi
(O to 1380 kPa). 5S5123 or 6V4161
Hydraulic Testing Group.
NOTE: It is possible to hear the sound of air leakage. Air
leakage can be seen when water with soap (soapy
water) is put on the connections, valves and hoses.
1.
Start the engine and let the air pressure go up to
the cutout pressure. Stop the engine.
NOTE: The governor cutout pressure is to be 125 + 5
psi (860 + 35 kPa). If cutout pressure is not correct, see
the subject, AIR COMPRESSOR GOVERNOR.
2.
Check for leakage in the hoses, lines and con-
nections from the air compressor and governor to
the tractor reservoirs.
3.
Check for leakage in the hoses, lines and con-
nections from the tractor reservoirs to the brake
control valve, emergency pilot valve and accessory
circuit.
4.
Check for leakage in the brake control valve.
NOTE: If the air pressure gets below 100 psi (690 kPa)
(cut-in pressure), start and run the engine until the air
pressure goes up to the cutout pressure.
5.
Check for leakage in the hoses, lines and
connections from the brake control valve to the seat
suspension, differential lock salve and emergency
and parking brake control valves.
6.
Check for leakage in the valves and switches.
7. Check
for
leakage
in
the
hoses,
lines
and
connections from the brake control valve to the
parking and emergency brake control valves.
8. Move the knob on the parking and emergency brake
control valves to the OFF position (pushed in).
2-145
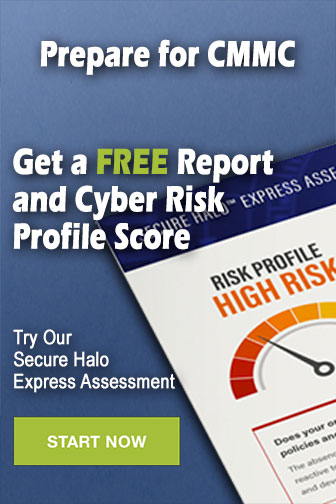