Tighten bolts (9) finger tight. Tighten bolt (10)
lightly. Tighten bolt (11). Loosen, then tighten bolts (9)
and bolt (10). Spin boring bar (5) during all tightening
operations. Repeat abode procedure if boring bar (5)
binds.
BOLT LOCATION
9. Bolts (two). 10. Bolt. 11. Bolt.
Remove original bearing caps and centering
rings. Mark news caps to correspond with numbers on
saddle and install new service caps. Mark caps and
saddles "OS" for oversize ne\fs14 t to location number.
Be sure to install new bolts. Put engine oil on
bolt threads and washer face. Tighten bolts in number
sequence to 30 + 3 lb. ft. (40 + 4 N. m). put a mark
on
each bolt and cap. Tighten all bolts by number from
mark an added 120 + 5°.
BOLT TIGHTENING SEQUENCE
(Typical Example)
Bolt torsion bar assembly (12) loosely to opposite
end of block from which boring bar will be driven. Install
feed assembly (14) into boring bar and tighten setscrew
(13). Slide feed assembly (14) onto torsion bar
assembly (12) and tighten bolt (15). Tighten bolt (16)
finger tight. Boring bar must slide in and out freely after
these tightening operations. Tighten thumbscrew (17).
FEED ASSEMBLY INSTALLED
12. 1P2369 Torsion Bar Assembly. 13. Setscrew.
14.
1P2365 Feed Assembly. 15. Bolt. 16. Bolt. 17.
Thumbscrew.
Place adapter (18) into boring bar and tighten
setscrew (19).
ADAPTER INSTALLED
18. 1P2364 Adapter. 19. Setscrew.
To set tool in tool holder. Set micrometer (21) to
3. 7075 in. (94. 171 mm). Place centering ring ( I ) on
the 1P2370 Micrometer Bracket Assembly. Move
micrometer (2 1) until spindle (20) contacts centering ring
(1). Tighten bolt (22). Back off micrometer thimble and
recheck micrometer setting. Repeat above steps until
micrometer setting is accurate.
SETTING MICROMETER
1. 1 P2344 Centering Ring. 20. Micrometer spindle.
21. Micrometer. 22. Bolt.
3-376
.
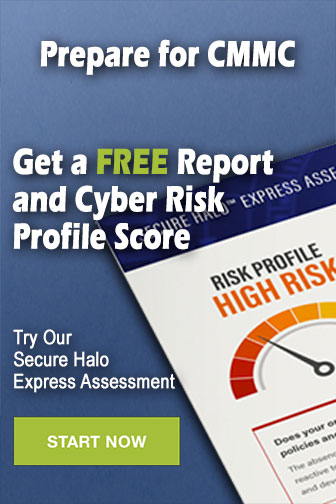